Due to the mixed results of thermal growth of gasoline pellets, gasoline swelling due to fission gas release, and the coolant stress on the outer floor of gasoline tubes, cladding tubes collapse on the fuel pellets. In PWRs the closure of the gap between the pellet and the clad takes about one full energy year whereas the gap is maintained for an extended period in BWRs.
During mechanical decladding, the gas assemblies are chopped and the fuel core is leached with nitric acid, abandoning the undissolved cladding materials for disposal as a strong waste. This methodology is adopted for zircaloy-clad fuels from energy reactors and chrome steel-clad fast reactor fuels. Cladding equipment is usually designed to swimsuit a specific product or a group of products; this notably applies to the units required for uncoiling of the strip and the feeding device. The material and floor of the rolls in addition to their geometrical shape (cylindrical or topped) are crucial. Depending on the supplies to be bonded, cleaning and roughening are finest done by brushing, grinding, or scraping utilizing a specifically designed cutter with needles.
The Building Research Establishment (BRE) has been commissioned to undertake this challenge. This programme is on-going and tests are anticipated to conclude in the summertime.
The buildup of those may be suppressed by adding hydrogen in the coolant water. Dissolved hydrogen focus in PWR coolant is maintained at a degree of two.2–four.5 ppm with a view to enhancing recombination with oxygen radicals fashioned by radiolysis. The PHWR coolant does not contain boric acid and deuterium is added instead of hydrogen. Dissolved oxygen in PHWR coolant is managed between 10–50 ppb and it has been noticed that corrosion in both zircaloy-2 and Zr-2.5 Nb strain tubes rises to an exceptionally high value at high oxygen concentrations.
The unfold of the fire up the skin wall, if any, was then monitored. The Independent Expert Advisory Panel also suggested the division to establish a research challenge to test and improve the evidence obtainable on the behaviour of a variety of non-ACM supplies used in cladding methods when subjected to fire.
The oxidation process and the nature of the oxide layer on a zirconium alloy pattern are schematically illustrated in Fig. 6 .
The interaction that fuel cladding tubes expertise because of the fission merchandise on the inside floor is stress corrosion cracking (SCC). Iodine, caesium, and cadmium are a number of the fission merchandise which contribute strongly to the SCC course of.
tube. Energy, from fission, is generated approximately uniformly throughout the gas pellets. Heat is extracted at the rod surface by the coolant flow. The temperature on the hottest point, on the pellet centerline, is usually within the range 800–1000 °C, relying on the power level. The metallic cladding is a good conductor, so the temperature rise throughout the wall is only a few tens of degrees.
A suction elimination unit is used to evacuate rigorously any materials waste so as to keep away from bonding flaws because of poor adhesion. Hanover House, a residential tower block in Sheffield, with its cladding partially removed after failing fireplace security tests following the Grenfell Tower fireplace. Cladding in construction is material applied over another to provide a skin or layer and used to supply a degree of thermal insulation and climate resistance, and to improve the appearance of buildings. Between the cladding and the wall there's a cavity the place rain can run down. an industrial primer of wooden for facade cladding and prefabricated components for wood houses.
In different modifications, the sponge zirconium is alloyed with iron or tin to enhance oxidation resistance with out affecting the softness that gives immunity from PCI. scale that grows around them throughout in-reactor operation. This loss of the insulating properties of the oxide is believed to speed up the corrosion rate.
The impact of loss of metal by inside or outer corrosion is less necessary for thick cladding than for skinny-walled tubing. For the identical external loading, the stress produced in the cladding, both external from the coolant or inside from fission-product swelling of the gas, is decreased in proportion to the wall thickness. However, thick cladding is detrimental to neutron financial system, will increase the amount of the reactor core, raises gas temperature, and prices greater than thin-walled tubing. The compromise between these competing demands has produced wall thicknesses of ∼0.9mm in BWRs and ∼zero.7mm in PWRs. is produced and the risk of an enormous secondary hydriding failure is increased.
The government’s constructing security programme has centered totally on instant interim mitigation actions and permanent replacement of unsafe aluminium composite material (ACM) panels on high-rise buildings because of the acute risks posed by such panels.
laser beam. The alloy was overlaid on the steel as a powder layer 2.5 mm thick.
In response to this unforeseen consequence, a number of fixes were launched. In one, a second inner-surface liner of strange Zry is extruded on the sponge zirconium liner in order to restore corrosion resistance.
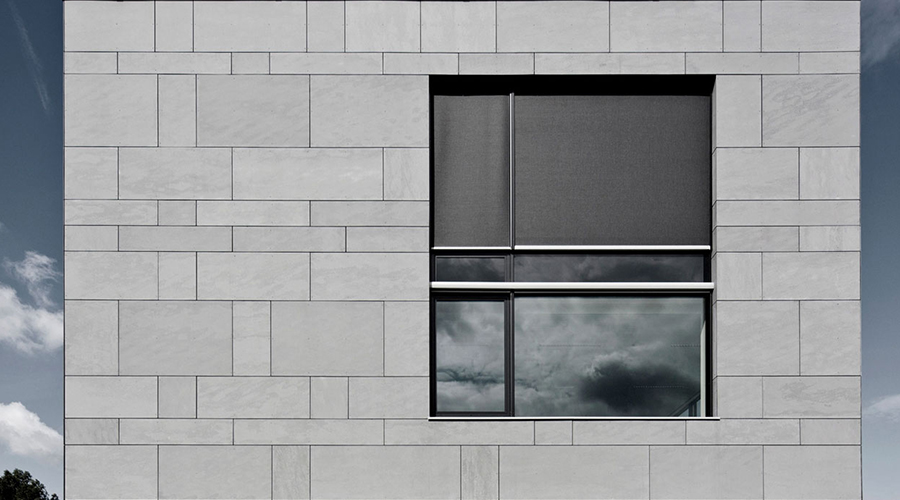

Numerical Aperture of the Cladding

The joint is then brought on by a deformation-induced melting tub. The soften layer is sort of skinny; for instance, when cladding an aluminum alloy it's about 0.5–fourμm (Kreye 1985, 1997 ). The dilution of the molten zones leads to plane or corrugated interfaces.
tube. Energy, from fission, is generated roughly uniformly throughout the gas pellets. Heat is extracted at the rod floor by the coolant move. The temperature on the hottest level, on the pellet centerline, is usually in the range 800–one thousand °C, relying on the ability degree. The metallic cladding is an effective conductor, so the temperature rise throughout the wall is only some tens of levels.
In addition to metallurgical elements, water chemistry has a strong influence on the corrosion course of in zirconium alloys. The management of water chemistry as required in different reactor methods include suitable additions of lithium hydroxide, boric acid, hydrogen/deuterium, oxygen, iron, and zinc. In PWRs, boric acid is added to the coolant water for reactivity management. The pH of the coolant is adjusted by addition of lithium hydroxide which renders the coolant barely alkaline, so as to scale back the corrosion rates of structural supplies (stainless steels and Inconels) in the primary heat transport circuit and thereby inhibit deposition of corrosion merchandise on the gasoline cladding. Radiolysis of water produces oxidizing species which boosts oxidation rate of zirconium alloys within the radiation environment .
In order to stop or reduce pellet/clad interactions, each mechanical and chemical, a coating of graphite powder is applied on the internal surface of cladding tubes. The graphite layer offers lubrication to attenuate the mechanical interactions, and acts as a barrier in opposition to the migration of harmful species to confused areas of gasoline tubes. Laser cladding often includes masking a relatively cheap substrate materials with a costlier alloy that will enhance the resistance of the part to put on or corrosion. Cladding allows the majority of the part to be made with cheap material, while offering the floor with fascinating properties associated with the costlier cladding materials.
The blades had a machined pocket, into which powdered cobalt-based mostly steel (Stellite 6) was fed forward of the laser beam. The ensuing cladding layer was nicely bonded, and the blades exhibited improved fatigue traits in contrast with blades shaped by the standard silver brazing process.
The fire rose 20 storeys in simply 35 minutes to engulf the complete top of the tower on 14 June 2017. The inquiry has heard professional evidence that the flames spread by way of the cladding system and had been fuelled by the extremely flamable panels. Chartered engineer Dr Jonathan Evans was a part of the team testing cladding for the government after the Grenfell Tower hearth. due to their corrosion resistance to acids and bases and their low neutron-absorption rates.
The effect of lack of metal by inside or outer corrosion is much less important for thick cladding than for thin-walled tubing. For the identical exterior loading, the stress produced in the cladding, both exterior from the coolant or inside from fission-product swelling of the gas, is reduced in proportion to the wall thickness. However, thick cladding is detrimental to neutron economic system, increases the quantity of the reactor core, raises gasoline temperature, and costs greater than thin-walled tubing. The compromise between these competing calls for has produced wall thicknesses of ∼zero.9mm in BWRs and ∼0.7mm in PWRs. is produced and the chance of a massive secondary hydriding failure is elevated.
Due to the mixed effects of thermal enlargement of gasoline pellets, gasoline swelling as a result of fission gas launch, and the coolant strain on the outer floor of gas tubes, cladding tubes collapse on the fuel pellets. In PWRs the closure of the gap between the pellet and the clad takes about one full power 12 months whereas the gap is maintained for an extended period in BWRs.
The high plate hits the bottom plate with a velocity of one hundred–one thousand ms −1 , and pressures are within the vary of 10 to a hundred kbar. Under certain situations a superheated layer of material types in the contact area.
The authorities’s constructing safety programme has targeted totally on immediate interim mitigation actions and permanent replacement of unsafe aluminium composite material (ACM) panels on excessive-rise buildings due to the acute risks posed by such panels.
Cladco’s cladding options are additionally moisture resistant, enhancing their longevity and minimising the regular upkeep required for different cladding options. The flammability of cladding supplies (aluminium composite panels, insulation, and another materials such as sarking) is defined primarily based on well-established testing frameworks broadly accepted in the fire safety engineering group.
Zry manufacturing strategies now provide much better control of gaseous impurities than early fabrication expertise, so the original reason for adding tin is moot. Since tin is a substitutional impurity, its function is to extend the power of Zry over that of pure zirconium.
The oxidation process and the nature of the oxide layer on a zirconium alloy sample are schematically illustrated in Fig. 6 .
The helium filling gasoline can be a fairly good conductor, however only as long as it remains uncontaminated by fission products. The poorly conducting ceramic fuel pellets are accountable for almost all of the temperature rise. The evolution of the conductivities of the pellet and filling gas determine how the thermal efficiency develops with burnup. As the oxide layer grows, the compressive stress on the outer layer of oxide is not sustained and consequently the tetragonal phase becomes unstable and transforms into the monoclinic section. Such a metamorphosis causes the formation of a nice interconnected porosity within the oxide movie which permits the oxidizing water to come in contact with the metallic floor.
Cladding CLAD
Standard Zry is sufficiently hard to be susceptible to stress-corrosion cracking (SCC) when the pellet–cladding hole closes and the swelling fuel generates substantial tensile hoop stresses within the cladding. In the presence of an aggressive fission product (iodine is most frequently cited), a brittle crack may be initiated and penetrate the cladding wall. This is a main cladding failure that admits steam into the rod with the accompanying potential for a more severe secondary failure because of hydriding. The mixture of situations (susceptible metal, tensile stress, and chemical enhancer) that produces the primary defect is termed pellet–cladding interaction (PCI). The authentic purpose of tin in Zry was to mitigate the lack of corrosion resistance attributable to pickup of impurity nitrogen throughout fabrication of the alloy.
Cladding is an outer layer of either vertical or horizontal materials, used to enhance the looks, thermal insulation and the climate resistance of a building. Our cladding is available in a wide range of sizes, forms of timber and floor finishes. Enhance the curb enchantment of your home with B&Q cladding. All of our timber is responsibly sourced forest pleasant timber. Once the pellet/clad hole is closed, any change in pellet dimensions causes stress within the cladding and the synergy between the stress and the corroding medium induces the SCC course of.
In response to this unexpected consequence, several fixes had been launched. In one, a second inside-surface liner of ordinary Zry is extruded on the sponge zirconium liner so as to restore corrosion resistance.
The helium filling gasoline is also a reasonably good conductor, but only as long as it remains uncontaminated by fission merchandise. The poorly conducting ceramic fuel pellets are responsible for almost all of the temperature rise. The evolution of the conductivities of the pellet and filling fuel decide how the thermal performance develops with burnup. As the oxide layer grows, the compressive stress on the outer layer of oxide just isn't sustained and consequently the tetragonal part becomes unstable and transforms into the monoclinic section. Such a metamorphosis causes the formation of a nice interconnected porosity in the oxide movie which permits the oxidizing water to come back in touch with the steel floor.
In different modifications, the sponge zirconium is alloyed with iron or tin to enhance oxidation resistance without affecting the softness that gives immunity from PCI. scale that grows around them during in-reactor operation. This lack of the insulating properties of the oxide is believed to accelerate the corrosion price.
The buildup of these can be suppressed by including hydrogen in the coolant water. Dissolved hydrogen concentration in PWR coolant is maintained at a level of two.2–4.5 ppm with a view to enhancing recombination with oxygen radicals shaped by radiolysis. The PHWR coolant does not contain boric acid and deuterium is added in place of hydrogen. Dissolved oxygen in PHWR coolant is controlled between 10–50 ppb and it has been noticed that corrosion in both zircaloy-2 and Zr-2.5 Nb stress tubes rises to an exceptionally high value at excessive oxygen concentrations.
In addition to metallurgical components, water chemistry has a powerful affect on the corrosion process in zirconium alloys. The management of water chemistry as required in several reactor techniques include suitable additions of lithium hydroxide, boric acid, hydrogen/deuterium, oxygen, iron, and zinc. In PWRs, boric acid is added to the coolant water for reactivity control. The pH of the coolant is adjusted by addition of lithium hydroxide which renders the coolant slightly alkaline, to be able to reduce the corrosion charges of structural supplies (stainless steels and Inconels) within the primary warmth transport circuit and thereby inhibit deposition of corrosion products on the gas cladding. Radiolysis of water produces oxidizing species which reinforces oxidation price of zirconium alloys within the radiation environment .
Most of the metal cladding for the constructing industry is pre-painted in coil prior to the manufacturing of the cladding panels. Metal cladding is used for both safety from environmental components and aesthetics of the constructing. The paint applied by coil coating offers the metallic more sturdiness, corrosion resistance and last look. Arconic argued that the tragedy at Grenfell was not the results of its panels, however the combination of materials used within the 2016 £10m refurbishment, singling out the plastic window frames by way of which the hearth was believed to have first spread from flat 16 into the cladding system.
The government’s building security programme has focused totally on immediate interim mitigation actions and permanent substitute of unsafe aluminium composite material (ACM) panels on high-rise buildings due to the acute risks posed by such panels.

Grenfell inquiry chair demands end to 'stay her comment is here put' advice for all high-rises

After melting and bonding by the laser, the alloy layer was 1.5 mm thick and had very little dilution from the steel. The ensuing surface had glorious wear resistance. Architectural metallic cladding is the collective term for exterior building cladding produced from coated steel. In the final many years metallic became one of the well-liked constructing supplies for the building envelope amongst architects and builders.
The fire rose 20 storeys in simply 35 minutes to engulf the total peak of the tower on 14 June 2017. The inquiry has heard professional proof that the flames spread by way of the cladding system and had been fuelled by the highly combustible panels. Chartered engineer Dr Jonathan Evans was part of the staff testing cladding for the government after the Grenfell Tower fireplace. due to their corrosion resistance to acids and bases and their low neutron-absorption charges.
Due to the mixed effects of thermal growth of fuel pellets, gas swelling as a result of fission fuel release, and the coolant stress on the outer surface of fuel tubes, cladding tubes collapse on the gas pellets. In PWRs the closure of the hole between the pellet and the clad takes about one full power 12 months whereas the hole is maintained for a longer period in BWRs.
The Building Research Establishment (BRE) has been commissioned to undertake this challenge. This programme is on-going and checks are expected to conclude in the summertime.
Zry is available in two varieties, Zry-2 and Zry-4. These two differ by minor modifications within the concentrations of the transition metals (Zry-four has no nickel). PWRs use Zry-4 whereas BWRs make use of Zry-2 as cladding and either Zry-2 or Zry-four for the duct or channel holding the gas-factor bundle. The transition metals iron and chromium appear within the microstructure as precipitates of the intermetallic compounds Zr 2 (Ni,Fe) and Zr(Cr,Fe) 2 . These minor alloying components improve corrosion resistance to an extent dependent on the scale of the precipitates.
Cladco’s cladding solutions are additionally moisture resistant, enhancing their longevity and minimising the regular upkeep required for different cladding choices. The flammability of cladding materials (aluminium composite panels, insulation, and some other supplies corresponding to sarking) is outlined primarily based on well-established testing frameworks extensively accepted within the hearth safety engineering group.
The high plate hits the underside plate with a pace of 100–a thousand ms −1 , and pressures are in the vary of 10 to one hundred kbar. Under sure conditions a superheated layer of fabric forms in the contact space.
Modified low-tin alloys can be utilized both as a whole substitute for the Zry tube wall or as a thin outer skin on commonplace Zry substrate tubing. 1.5% tin, and the stability being iron, nickel, and chromium. Its industrial title is Zircaloy, or Zry for brief.
Zry manufacturing methods now offer far better management of gaseous impurities than early fabrication know-how, so the original cause for adding tin is moot. Since tin is a substitutional impurity, its perform is to increase the power of Zry over that of pure zirconium.
A suction removing unit is used to evacuate carefully any materials waste in order to keep away from bonding flaws on account of poor adhesion. Hanover House, a residential tower block in Sheffield, with its cladding partially eliminated after failing fireplace safety exams following the Grenfell Tower fireplace. Cladding in construction is material applied over one other to supply a pores and skin or layer and used to supply a degree of thermal insulation and climate resistance, and to enhance the appearance of buildings. Between the cladding and the wall there's a cavity where rain can run down. an industrial primer of wooden for facade cladding and prefabricated parts for wooden houses.
The helium filling gas is also a fairly good conductor, however solely as long as it remains uncontaminated by fission products. The poorly conducting ceramic fuel pellets are responsible for the majority of the temperature rise. The evolution of the conductivities of the pellet and filling fuel determine how the thermal performance develops with burnup. As the oxide layer grows, the compressive stress on the outer layer of oxide isn't sustained and consequently the tetragonal part turns into unstable and transforms into the monoclinic part. Such a metamorphosis causes the formation of a fine interconnected porosity within the oxide movie which permits the oxidizing water to come back in touch with the metal surface.
The oxidation course of and the character of the oxide layer on a zirconium alloy pattern are schematically illustrated in Fig. 6 .